Discover What is Porosity in Welding and Its Result on Structural Integrity
Understanding Porosity in Welding: Checking Out Reasons, Impacts, and Prevention Strategies
Porosity in welding is a consistent challenge that can considerably affect the high quality and integrity of welds. As experts in the welding sector are well conscious, understanding the reasons, effects, and prevention techniques connected to porosity is crucial for accomplishing robust and reliable welds. By diving into the source of porosity, analyzing its damaging results on weld quality, and checking out reliable prevention techniques, welders can enhance their knowledge and abilities to produce top quality welds consistently. The intricate interaction of elements adding to porosity calls for a detailed understanding and a proactive strategy to guarantee effective welding outcomes.
Typical Reasons For Porosity
Contamination, in the form of dirt, oil, or corrosion on the welding surface area, develops gas pockets when heated up, leading to porosity in the weld. Incorrect shielding takes place when the securing gas, commonly used in processes like MIG and TIG welding, is unable to totally shield the molten weld swimming pool from reacting with the surrounding air, resulting in gas entrapment and succeeding porosity. Additionally, insufficient gas coverage, often due to incorrect flow prices or nozzle positioning, can leave components of the weld unguarded, enabling porosity to create.
Effects on Weld High Quality
The existence of porosity in a weld can dramatically compromise the general high quality and stability of the welded joint. Porosity within a weld produces voids or dental caries that weaken the structure, making it much more vulnerable to breaking, deterioration, and mechanical failure.
Moreover, porosity can prevent the performance of non-destructive testing (NDT) techniques, making it testing to discover various other flaws or interruptions within the weld. This can cause considerable security problems, especially in critical applications where the architectural integrity of the welded elements is critical.
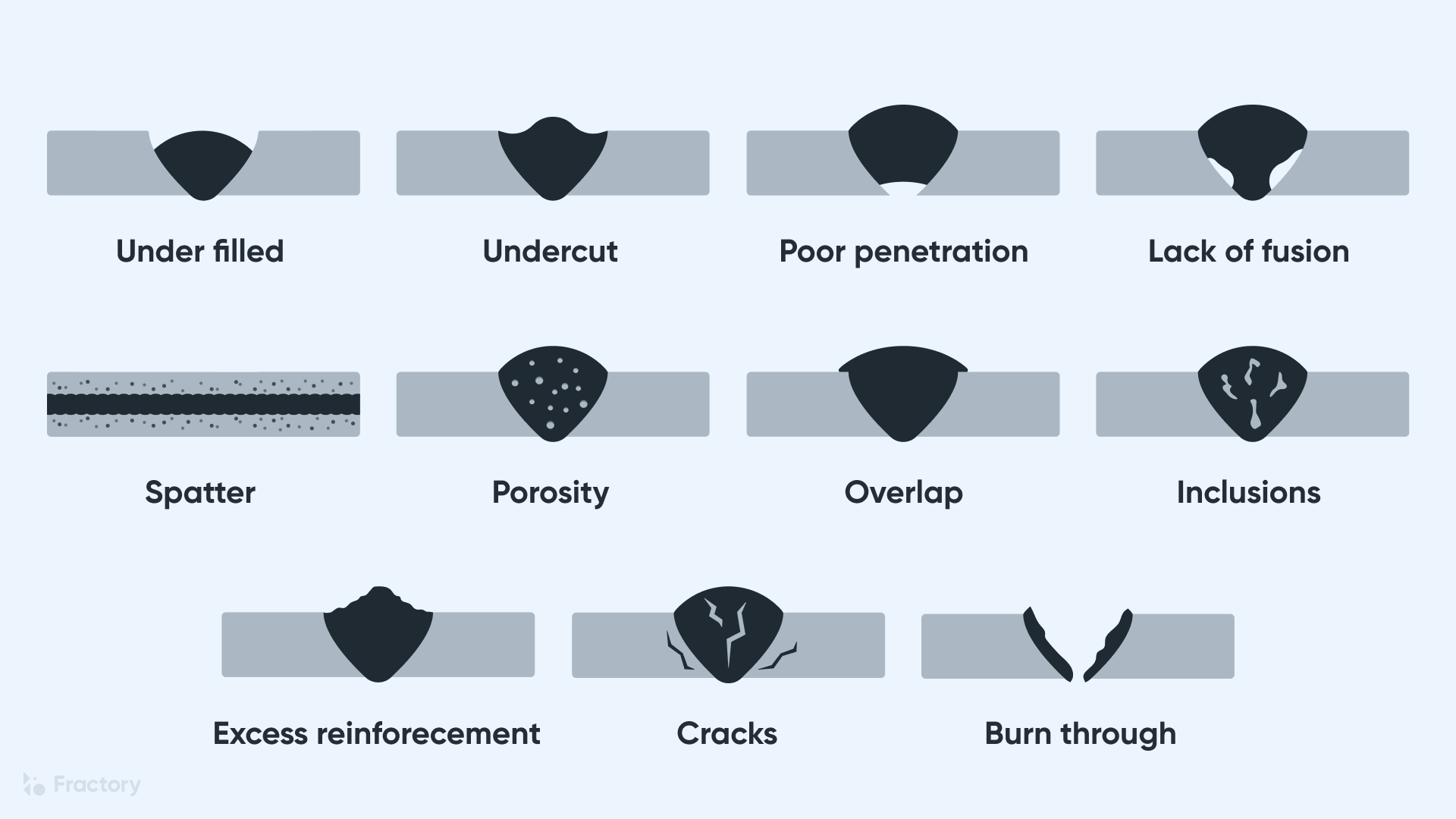
Prevention Techniques Review
Given the damaging effect of porosity on weld quality, effective avoidance methods are important to preserving the architectural integrity of bonded joints. Among the main prevention strategies is thorough cleaning of the base products before welding. Impurities such as oil, oil, rust, and wetness can add to porosity, so guaranteeing a tidy job surface area is vital. Appropriate storage space of welding consumables in completely dry conditions is additionally important to avoid wetness absorption, which can cause gas entrapment throughout welding. Additionally, picking the suitable welding criteria, such as voltage, current, and travel speed, can assist lessen the danger of porosity formation. Making certain sufficient protecting gas flow and protection is an additional critical avoidance strategy, as inadequate gas coverage can lead to atmospheric contamination and porosity. Finally, proper welder training and certification are important website here for executing safety nets efficiently and regularly. By integrating these prevention strategies into welding methods, the incident of porosity can be substantially lowered, resulting in more powerful and more dependable bonded joints.
Relevance of Proper Shielding
Proper protecting in welding plays an essential role in stopping atmospheric contamination and guaranteeing the stability of welded joints. Shielding gases, such as argon, helium, or a blend of both, are generally made use of to safeguard the weld pool from responding with components in the air like oxygen and nitrogen. When these responsive elements enter call with the hot weld pool, they can create porosity, causing weak welds with lowered mechanical properties.
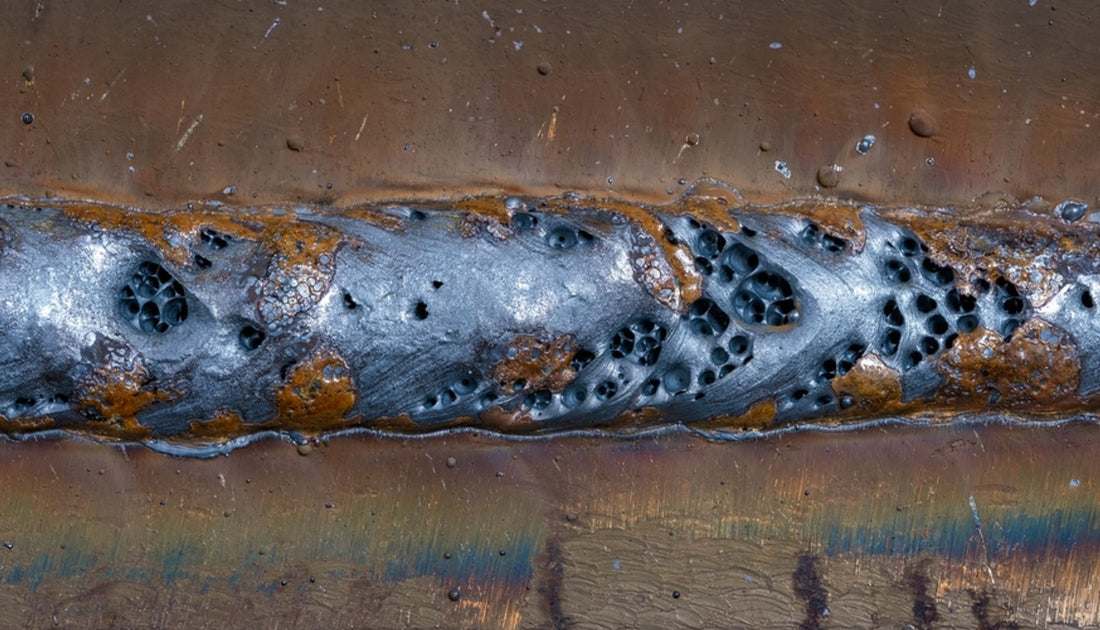
Poor shielding can cause different problems like porosity, spatter, and oxidation, compromising the architectural honesty of the bonded joint. Adhering to appropriate protecting methods is important to generate premium welds with marginal flaws and make sure the long life and integrity of the bonded components.
Tracking and Control Approaches
Exactly how can welders effectively monitor and manage the welding procedure to ensure optimum results and avoid defects like porosity? By constantly keeping track of these variables, welders can identify deviations from the optimal conditions and make instant adjustments to prevent porosity formation.

Additionally, executing correct training programs for welders is important for monitoring and regulating the welding process efficiently. What is Porosity. Enlightening welders on the significance of maintaining consistent specifications, such as correct gas shielding and take a trip rate, can help prevent porosity concerns. Regular assessments and certifications can likewise guarantee that welders are skillful in tracking and controlling welding processes
Moreover, using automated welding systems can these details enhance surveillance and control capacities. These systems can specifically regulate welding criteria, decreasing the chance of human mistake and making certain constant weld quality. By combining sophisticated surveillance technologies, training programs, and automated systems, welders can effectively check and regulate the welding procedure to minimize porosity flaws and attain high-grade welds.
Final Thought
